Áß°í±â°è,Áß°í°øÀÛ±â°è,Áß°í»ê¾÷±â°è,Áß°í±â°è±Þ¸Å °Ô½ÃÆÇ |
|
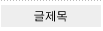 |
Cu °øÁ¤±â¼úÀÇ °³¿ä |
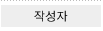 |
QAS Áß°í±â°è ÇѰø»ê¾÷±â°è |
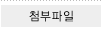 |
- |
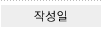 |
2008-03-18 ¿ÀÈÄ 8:26:48 |
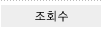 |
7246 |
|
|
Cu °øÁ¤±â¼úÀÇ °³¿ä
Cu IC ¹è¼± °øÁ¤±¸Á¶¿¡¼ CuÁõÂø°ú polishing ¹× Cu ¼¼Á¤°øÁ¤ÀÇ ¼¼ºÎÀûÀÎ ¼³¸íÀ» Çϱâ¾Õ¼,
Cu dual damascene±¸Á¶¸¦ Çü¼ºÇϱâÀ§Çؼ Àü¹ÝÀûÀÎ °øÁ¤¼ø¼¸¦ ¿ì¼±ÀûÀ¸·Î °£´ÜÈ÷ »ìÆìº¸´Â°ÍÀº Áß¿äÇÏ´Ù.
ÀÌ·¯ÇÑ °øÁ¤¼ø¼´Â ¾Æ·¡¿¡ ³ª¿µÇ¾î ÀÖ´Ù.±×¸®°í ¶ÇÇÑ ±×¸² 16-11¿¡ µÇ½ÃÈ µÇ¾îÀÖ´Ù.
1. ºñ Àüµµ¼º È®»ê ¹æÁö¸· ÁõÂø
2. Dielectric Layer(Àý¿¬¸·) ÁõÂø
3. Dual Damascene°øÁ¤¿¡¼ÀÇ Àý¿¬¸· ½Ä°¢( Via, Trench, È®»ê¹æÁö¸· ½Ä°¢)
4. Àüµµ¼º È®»ê ¹æÁö¸· ÁõÂø
5. Cu seed ÁõÂø
6. Cu Àü±âµµ±ÝÁõÂø( Àü±âµµ±ÝÁõÂø ÈÄ ¾î´Ò¸µ °øÁ¤)
7. Cu¿Í È®»ê¹æÁö¸· CMP
8. Cu ¼¼Á¤°øÁ¤
9. ºñ Àüµµ¼º È®»ê ¹æÁö¸· ÁõÂø
ÀÌ·¯ÇÑ °øÁ¤Àº ¿þÀÌÆÛ Àü¸é(»çÀü¿¡ CMP°øÁ¤¿¡ÀÇÇØ ÆòÅºÈ µÇ°í, ÇѰ³ ȤÀº ±× ÀÌ»óÀÇ ¹è¼±ÃþÀÌ ÀÌ¹Ì ¸¸µé¾îÁø ¿þÀÌÆÛ)¿¡ ´ëÇØ
ºñ Àüµµ¼º È®»ê ¹æÁö¸· ÁõÂø(¿¹: PECVD¿¡ÀÇÇÑ ½Ç¸®ÄÜ ³ªÀÌÆ®¶óÀ̵åÁõÂø)¿¡¼ºÎÅÍ ½ÃÀ۵ȴÙ.
´ÙÀ½ °øÁ¤Àº ILD(Ãþ°£ Àý¿¬¸·)ÀÌ ÁõÂøµÈ´Ù. ¸®¼Ò±×·¡ÇÇ °øÁ¤À» »ç¿ëÇÏ¿© dual-damascene ±¸Á¶ÀÇ via¿Í trench¸¦ Á¤¿Çϰí,
±×ÈÄ °Ç½Ä½Ä°¢°øÁ¤¿¡ ÀÇÇØ ½Ä°¢µÈ´Ù. (À̰ÍÀº °¢ ½Ä°¢°øÁ¤ÈÄ Æ÷Åä·¹Áö½ºÆ®ÀÇ Á¦°Å °øÁ¤À» Æ÷ÇÔÇÏ¿©, 2¹øÀÇ ¸®¼Ò±×·¡ÇǰøÁ¤°ú ½Ä°¢°øÁ¤À» ¿ä±¸ÇÑ´Ù.)
Via ¾Æ·¡ÀÇ SiN È®»ê¹æÁö¸· ¿ª½Ã 2¹øÂ° ½Ä°¢°øÁ¤ÀÌ ÁøÇàµÇ´Âµ¿¾È µå·¯³ª°í, ±Ý¼Ó¹è¼±ÃþÀÇ ³ëÃâÀÌ ¹è¼±±¸Á¶ÀÇ Ãþ¿¡ Çü¼ºµÈ´Ù.
±× ´ÙÀ½ Àüµµ¼º È®»ê ¹æÁö¸·/Á¢Âø¸·(adhesion layer)ÀÌ waferÀ§¿¡ ÀϹÝÀûÀ¸·Î collimated, long-throw ȤÀº ÀÌ¿ÂÈ ±Ý¼Ó PVD¿¡ ÀÇÇØ¼ ÁõÂøµÈ´Ù.
ÀÌ·¯ÇÑ È®»ê ¹æÁö¸·/Á¢Âø¸·(adhesion layer)ÀÇ ¿ªÇÒÀ» ¼öÇàÇÏ´Â ¿©·¯°¡Áö ´Ù¾çÇÑ ¹°ÁúÀº Ta, TaN, TaSiN, TiN, TiSiN, WN ¹× WSiNÀ» Æ÷ÇÔÇÑ´Ù.
ÈÄ¼Ó °øÁ¤ÀÎ Cu Àü±âµµ±Ý °øÁ¤¿¡¼ ³·Àº Àü±âÀû ÀúÇ×path¸¦ Á¦°øÇϱâ À§ÇØ Cu seed ¸·À» È®»ê ¹æÁö¸·/Á¢Âø¸·(adhesion layer)À§¿¡ ÁõÂøÇÑ´Ù.
Cu seed¸·Àº È®»ê ¹æÁö¸·/Á¢Âø¸·(adhesion layer)À» Á¤ÂøÇÒ¶§ »ç¿ëÇÑ µ¿ÀϰøÁ¤ÀÎ PVD°øÁ¤¿¡ ÀÇÇØ Áø°ø»óŸ¦ ±úÁö¾Ê°í in-situ¹æ½ÄÀ¸·Î ÁõÂøÇÑ´Ù.
Cu¸¦ ÀÌ¿ëÇÑ Trench¿Í via ä¿òÀÇ °øÁ¤ÀÇ ¿Ï¼ºÀº Cu Àü±âµµ±Ý¿¡ ÀÇÇØ ³¡ÀÌ ³´Ù.
ÀÌ·¯ÇÑ CuÀü±âµµ±Ý°øÁ¤Àº ´ÙÀ½ÀÇ ¿µÇâÀ» °¡Áø´Ù.
a) ÁõÂø °áÇÔ¾øÀÌ recessed(¹è¼±À» À§ÇØ µé¾î°£) ±¸¿ªÀ» ÁõÂøÇÒ¼öÀÖ´ÂÁö ¿©ºÎ(¿¹:±â°øseam, ÁõÂøÈÄ ÀÌ·¯ÇÑ ÁõÂø°áÇÔ¾øÀ»°Í)
b) ºü¸¥ ÁõÂø¼Óµµ
c) ¿þÀÌÆÛ Àü¹Ý¿¡ ´ëÇØ ±ÕÀÏÇÑ ÁõÂøµÎ²²¸¦ °¡Áú°Í(8" ¿þÀÌÆÛ¿¡¼ 5mm edge exclusion°í·ÁÇÏ¿©)
CMP °øÁ¤Àº via¿Í trench ¹ÛÀ¸·Î ÃʰúÁõÂøµÈ Cu¸¦ Á¦°ÅÇÏ´Â °øÁ¤ÀÌ´Ù.
±×·¯³ª recessÁö¿ª (¹è¼±À» À§ÇØ µé¾î°£)ÀÇ Cu´Â ³²´Â´Ù. CMP°øÁ¤Áß È®»ê¹æÁö¸·Àº Á¦°ÅµÇ¾î¾ß ÇÑ´Ù.
¿©±â¼ Cu¿Í È®»ê¹æÁö¸·ÀÇ ¿¬¸¶¼Óµµ´Â °°Àº¼Óµµ·Î ÁøÇàµÇ¾î¾ß ÇÑ´Ù.
ÀÌ·¯ÇÑ ÀÌÀ¯´Â TaȤÀº TaN°ú °°Àº ¹°ÁúÀº °æÇѹ°ÁúÀ̸ç, ±Ý¼Ó°£ ÈÇÕ¹°ÀÎ ¹Ý¸é, Cu´Â »ó´ëÀûÀ¸·Î ¿¬Çѹ°ÁúÀÌ´Ù.
CMP°øÁ¤ÀÌ ³¡³ ÈÄ¿¡ ¿þÀÌÆÛ´Â ¼¼Á¤µÇ¾î¾ß Çϸç, ¿þÀÌÆÛ Àü¹ÝºÎ¿Í ¿þÀÌÆÛ Èĸé°ú °¡ÀåÀÚ¸®ºÎ¿¡ Àý¿¬¸· Ç¥¸é¿¡ Cu ÀÜ·ù°¡ ¾ø¾î¾ßÇÑ´Ù.
¸¶Áö¸·À¸·Î, ºñ Àüµµ¼º È®»ê ¹æÁö¸·(CVD ½Ç¸®ÄÜ ³ªÀÌÆ®¶óÀ̵å)ÀÌ ¿þÀÌÆÛ Ç¥¸é¿¡ ÁõÂøµÈ´Ù.
À̰ÍÀº µå·¯³ ºÎºÐÀÇ CuÀÇ Ä¸È¿¡ ±â¿©ÇÑ´Ù.(Áï À̰ÍÀº µé¾î°£ ºÎºÐÀÇ Cu ¹è¼±ÀÇ ±¸Á¶ÀÇ Ä¸½¶È¸¦ ¿ÏÀüÈ÷ ÀÌ·é´Ù.
±×¸®ÇÏ¿© Cu ¹è¼±±¸Á¶´Â È®»ê¹æÁö¸· ¹°Áú¿¡ ÀÇÇØ ¸ðµç ¸éÀÌ µÑ·¯½ÎÀÌ°Ô µÈ´Ù.À̰øÁ¤ÀÇ ÀÚ¼¼ÇѰÍÀº º» ±³Àç 15Àå 15.6°ú 15.9¿¡ ÀÚ¼¼È÷ ´Ù·ç¾îÁ® ÀÖ´Ù.
(±×·¡¼ ¿©±â¼´Â ´Ù½Ã ¾ð±ÞµÇÁö ¾ÊÀ»°ÍÀÌ´Ù.)
±×·¡¼ ÀÌ·¯ÇÑ 4¹øÂ° ´Ü°èÀÇ °øÁ¤(È®»ê¹æÁö¸· ÁõÂø°ú ÀÌ¿¡ °üÇÑ ¹°ÁúµéÀÇ ¹°¼º)¿¡°üÇÑ ³íÀǰ¡ ½ÃÀ۵ǰí, ³²Àº ´Ù¸¥°øÁ¤ÀÇ ÀÚ¼¼ÇÑ »çÇ×ÀÌ ÁøÇàµÇ¾ú´Ù.
¡¡
16.2.1 ¾Ë·ç¹Ì´½¿¡¼ ±¸¸®¹è¼±À¸·ÎÀÇ º¯Ãµ
IC±â¼úÀÇ ¹è¼±°øÁ¤±â¼ú¿¡¼ÀÇ ±¸¸®ÀÇ Àû¿ëÀº 2°¡Áö¹æ¹ýÁß ÇѰ¡Áö¹æ¹ýÀÌ °¡´ÉÇÏ´Ù.
¾î¶²°øÁ¤Àº ´ÙÃþ¹è¼±ÀÇ ±¸Á¶¹°¿¡¼ ¾Ë·ç¹Ì´½:±¸¸®(W-Ç÷¯±×)¸¦ ¼±ÅÃÇØ¿Ô°í, »óºÎÃþ¿¡¿¡¼ ±¸¸®¹è¼±ÀÇ »ç¿ë¸¸ÀÌ Á¦ÇÑ µÇ¾îÁ®¿Ô´Ù.
¿¹¸¦µç´Ù¸é, ¾Ë·ç¹Ì´½:±¸¸®¹è¼±Àº 6Ãþ¹è¼±ÀÇ ¹è¼± ±¸Á¶¹°¿¡¼ 4ÃþÀÇ ÇϺΠ¹è¼±¿¡¼ »ç¿ëµÇ¾î Á³°í ±¸¸®´Â »óºÎ 2°³Ãþ¿¡¼ »ç¿ëµÇ¾ú´Ù.(±×¸²16-12 ÂüÁ¶)
TSMC¿Í °°Àº ´Ù¸¥°øÁ¤¿¡ ÀÇÇØ 4ÃþÀÇ ¾Ë·ç¹Ì´½ ¹è¼±Ãþ°ú 2°³ÀÇ ±¸¸®¹è¼±ÃþÀ¸·Î »ç¿ëµÇ¾ú´Ù.
»óºÎÀÇ ¾Ë·ç¹Ì´½¹è¼±°ú ÇϺÎÀÇ ±¸¸®¹è¼±»çÀÌÀÇ °áÇÕÀº ÅÖ½ºÅÙ Ç÷¯±× ȤÀº Cu-damascene °øÁ¤¿¡ »ç¿ëµÉ¼öÀÖ´Ù.
±×·¯³ª, ´Ù¸¥ Á¦Á¶ ȸ»ç´Â ¹è¼±±¸Á¶ Àüü¿¡¼ (ÄÜÅØÆ®È¦¿¡¼ »ç¿ëµÈ ÅÖ½ºÅÙ Ç÷¯±×¸¦ »ç¿ëÇÏÁö ¾Ê°í¼) ±¸¸®¹è¼±À» »ç¿ëÇϱâ·Î °áÁ¤ÇÏ¿´´Ù.
6Ãþ ±¸¸®¹è¼±±¸Á¶(ÅÖ½ºÅÙ Ç÷¯±×¸¦ »ç¿ëÇÏ´Â)¿Í °°Àº ¿¹´Â IBM¿¡ÀÇÇØ¼ Á¦¾ÈµÇ¾ú´Ù.(±×¸² 16-13À» ÂüÁ¶)
±×¸²16-14´Â 6Ãþ ±¸¸®¹è¼±±¸Á¶¸¦ SEMÀ» »ç¿ëÇÏ¿© º¸¿©Áִ°ÍÀÌ´Ù.(¶ÇÇÑ 12ÀåÀÇ ±×¸²12-16À» ÂüÁ¶)
¡¡
16.2.2 Damascene ¹è¼±±¸Á¶¿¡¼ÀÇ ±¸¸®ÁõÂøÀÇ ÇØ°áÃ¥
Ãþ°£ Àý¿¬¸·ÀÌ ÀûÃþµÈ Dual-damascene±¸Á¶¿¡¼ ±¸¸®ÀÇ ÁõÂøÀÇ Çâ»óÀº ¸Å¿ì Áß¿äÇϸç, À̰ÍÀº ¾î¶°ÇÑ ±â°ø°ú °áÇÔÀÌ ¾øÀÌ µÇ¾î¾ßÇÑ´Ù.
¾Æ·¡¿¡¼ºÎÅÍ À§·Î ½×¾Æ¿Ã¸®´Â(bottom-up, superfilling) ¹æ½ÄÀ¸·ÎºÎÅÍ ±¸¸®¸¦ ¹è¼±±¸Á¶¿¡ ä¿ï¼ö Àִ°ÍÀÌ Áß¿äÇÑ Á¡ÀÌ´Ù.
±×·¯³ª ¿ÏÀüÇÑ ±¸¸®ÀÇ Ã¤¿òÀº Àü±âµµ±ÝÁõÂø»Ó¸¸ ¾Æ´Ï¶ó Àý¿¬¸· ½Ä°¢°øÁ¤¿¡ ÀÇÇØ¼µµ ¿µÇâÀ» ¹ÞÀ¸¸ç,
È®»ê¹æÁö¸·°ú Cu-seed ÁõÂø°øÁ¤¿¡ÀÇÇØ¼µµ ¿µÇâÀ» ¹Þ´Â´Ù.
±×·¡¼, ÀÌ·¯ÇÑ ÁÖÁ¦´Â ´ÙÀ½¿¡ »ìÆìº¼ 3°¡Áö ´Ü¿ø¿¡¼ ´Ù·ç¾îÁú°ÍÀÌ´Ù.
16.3 ±¸¸®¹è¼±°øÁ¤À» À§ÇÑ È®»ê¹æÁö¸·
¾Õ¼ »ìÆìº»°Íó·³, Àý¿¬¹°Áú¿¡¼ È®»êµÇ´Â ±¸¸®¸¦ ¸·±âÀ§ÇØ È®»ê¹æÁö¸·ÀÌ »ç¿ëµÈ´Ù. ÀÌ È®»ê¹æÁö¸·¿¡ ÀÇÇØ ¸ðµç¸éÀÌ µÑ·¯½Î¿©¾ß ÇÑ´Ù.
ÇϺο¡ ³õ¿©Áø °æ¿ì´Â Cu°¡ ÁõÂø µÇ±â ÀÌÀü¿¡ ÁõÂøµÇ¾ú´Ù.(16.2Àý¿¡ ¸í½ÃµÈ°Íó·³)
ÀÌ Àý¿¡¼´Â Àüµµ¼º È®»ê¹æÁö¸·ÀÌ º¸¿©Á³´Ù. ±×¸®°í ¾Æ·¡¿Í °°Àº ÁÖÁ¦·Î ´Ù·ç¾îÁú°ÍÀÌ´Ù.
1. ±¸¸® Àü±âµµ±Ý °øÁ¤¿¡ ´ëÇÑ È®»ê¹æÁö¸·ÀÇ Á߿伺
2. PVD¿¡ ÀÇÇÑ damascene±¸Á¶¿¡ÀÇ È®»ê¹æÁö¸· ÁõÂø±â¼ú
3. È®»ê¹æÁö¸·ÀÇ Àç·áÀÎ Ta, TaN ¹× TaSiNÀÇ ¹°¼º
4. ±¸¸®¹è¼± °øÁ¤±â¼ú¿¡¼ ´Ù¸¥ È®»ê¹æÁö¸· ¹°Áú(CVD°øÁ¤À» Æ÷ÇÔÇÑ ÁõÂø¹°Áú)
¡¡
16.3.1 Damascene ±¸Á¶¿¡¼ ±¸¸®ÁõÂø ¿¡¼ÀÇ È®»ê¹æÁö¸·ÁõÂø °øÁ¤ÀÇ È¿°ú
Recap°øÁ¤À» ÇϱâÀ§ÇØ, ±¸¸®¹è¼±°øÁ¤¿¡¼ È®»ê¹æÁö¸·Àº ±¸¸®ÀÇ Àý¿¬¸·À¸·ÎÀÇ È®»êÀ» ¸·¾Æ¾ßÇϸç,
±¸¸®¿Í Àý¿¬¸·°úÀÇ ÁÁÀº Á¢Âø·ÂÀ» °¡Á®¾ß ÇÑ´Ù. °Ô´Ù°¡, È®»ê¹æÁö¸·Àº ¾ã¾Æ¾ß Çϸç ÀûÇÕ¼ºÀÌ ÀÖ¾î¾ß Çϸç, Àü±âÀûÀÎ ÀúÇ×ÀÌ ³·¾Æ¾ß ÇÑ´Ù.
ÁõÂøÀº ³·Àº¿Âµµ¿¡¼ ÀÌ·ç¾îÁö¸ç, ÆÄƼŬÀÇ ¹ß»ýÀÌ °ÅÀÇ ¾ø¾î¾ß ÇÑ´Ù.
È®»ê¹æÁö¸·Àº ¶ÇÇÑ Cu CMP ¹× Cu Àü±âµµ±Ý°øÁ¤°ú »óÈ£ÀûÀ̾î¾ßÇÑ´Ù.
¸¶Áö¸·À¸·Î, È®»ê¹æÁö¸·ÀÇ ÁõÂøÀº ±â°øÀÌ ¾ø´Â Cu¸¦ damascene±¸Á¶¿¡ ¿ÏÀüÈ÷ ä¿ï¼ö ÀÖ´Â ´É·ÂÀ» °¡Á®¾ßÇÑ´Ù.
ÀÌ·¯ÇÑ È®»ê¹æÁö¸·ÀÇ ÁõÂøÀº ¿¬¼ÓÀûÀ¸·Î ±×¸®°í ÀûÀýÇÑ µÎ²²¸¦ °¡Áö¸ç, overhang¾øÀÌ 25~30nmÀÇ µÎ²²¸¦ °¡Áö°í ÁõÂøµÇ¾î¾ßÇÑ´Ù.
È®»ê¹æÁö¸·ÀÇ ÁõÂøÀ» À§ÇØ »ç¿ëµÇ´Â PVD°øÁ¤Àº 2°¡Áö ¿ä¼Ò¿¡ ¿µÇâÀ» ÁØ´Ù. ±×¸®°í seed¿Í È®»ê¹æÁö¸· ÁõÂøÀ» À§ÇÑ PVD±â¼úÀº ´ÙÀ½ Àý¿¡ ±â¼úµÉ°ÍÀÌ´Ù.
¡¡
16.3.2 ±¸¸®¹è¼±¿¡¼ÀÇ È®»ê¹æÁö¸·ÀÇ ÁõÂø ±â¼ú¿¡ ´ëÇÑ °³¿ä
Cu°¡ ÁõÂøµÇ±â ÀüÀÇ Àüµµ¼º È®»ê¹æÁö¸· ÁõÂøÀº PVD¿Í CVD¹æ¹ý¿¡ ÀÇÇØ ÁõÂøµÇ¾î Áú¼ö ÀÖ´Ù.
PVDÀº 0.13¥ìmÀÇ °øÁ¤±îÁö¸¸ »ç¿ëµÇ¾î ¿Ô´Ù. ±×·¡¼ CVD·Î º¯ÈÇÒ°ÍÀÌ´Ù.
ÀÌ·¯ÇÑ ±â¼úÀÇ º¯È´Â PVD°øÁ¤¿¡ ÀÇÇÑ trench¿Í hole ³»¿¡¼ÀÇ ¹Ú¸·ÁõÂøµµ Æ÷ÇÔÇÑ´Ù.
±æÀÌ aÀÇ À°¸éü¸¦ °¡Áø contact ȦÀÌ »ó´ÜºÎ¿¡ ÀÖ´Ù°í °¡Á¤ÇÏÀÚ.(±×¸² 16-15ÂüÁ¶)
À̰ÍÀº 1:1ÀÇ aspect ratio¸¦ °¡Áö´Â contact holeÀ» Ç¥ÇöÇÑ´Ù.
ÀÌ·¯ÇÑ °æ¿ì¿¡, À°¸éü »ó´ÜºÎ ¿¡¼ a©÷(¸¸¾à contact holeÀÇ »ó´ÜºÎ°¡ ¿·Á ÀÖÁö¾Ê´Ù¸é) ÀÇ ¸éÀûÀ» °¡Áø ¹°Áú¿¡ ÀÇÇØ ¸éÀûÀÌ Ã¤¿öÁú°ÍÀÌ´Ù.
±×·¯³ª, ¸¸¾à contact holeÀÇ »ó´ÜºÎ°¡ ¿·Á ÀÖ´Ù¸é, 5a©÷°¡ ä¿öÁú°ÍÀÌ´Ù.
±×·¡¼ À̰æ¿ì´Â ÁõÂøµÇ´Â ¹°ÁúÀÌ contactȦÀÇ 5°³ÀÇ ³»ºÎ¸é¿¡ ºÐÆ÷ÇϰԵȴÙ.
ÁõÂøµÇ´Â µÎ²²´Â contact holeÀÇ ¿ÜºÎ ÆòÆòÇÑ Áö¿ªÀÇ µÎ²²ÀÇ 20%°¡ µÉ°ÍÀÌ´Ù.
¸í¹éÇϰÔ, ¸¸ÀÏ hole-openingÀÇ ºÎºÐÀÌ ¿©ÀüÈ÷ ³²¾Æ ÀÖ´Ù¸é, ±íÀ̰¡ Áõ°¡ÇÏ°Ô µÇ´Â°ÍÀÌ´Ù.
¶ÇÇÑ aspect-ratio°¡ Áõ°¡ÇÏ°Ô µÇ´Â°ÍÀÌ´Ù.(¿¹: ¸¸¾à contact holeÀÇ °³±¸¸éÀûÀÌ a©÷·Î À¯ÁöµÇ°í,
±íÀ̰¡ 2a °¡ µÈ´Ù¸é, aspect ratio´Â 2:1ÀÌ µÉ°ÍÀÌ´Ù.±×¸®°í ÁõÂø¹°Áú¿¡ ÀÇÇØ ÁõÂøµÉ ºÎºÐÀÇ ¸éÀûÀº 9a©÷°¡ µÉ°ÍÀÌ´Ù.
±×·¡¼ PVDÀǰæ¿ì¿¡´Â ¹è¼±È°øÁ¤À» À§ÇØ µé¾î°£ºÎºÐÀÇ aspect ratio°¡ Áõ°¡ÇÔ¿¡µû¶ó,ȸ·Î¹è¼±¿¡ ÁõÂøµÉ ¹°ÁúÀÌ ³ÐÀº Áö¿ªÀ¸·Î ÆÛÁ®
ÁõÂøµÉ °ÍÀÌ°í ´ÜÀ§¸éÀû´ç µÎ²²°¡ °¨¼ÒÇÏ°Ô µÈ´Ù. °Ô´Ù°¡, ÀÌ·± ȦÀÌ ÁõÂøÈÄ¿¡´Â ȦÀÇ »óºÎ ÆòÆòÇÑ ºÎºÐÀÌ ½Ä°¢µÇ°Å³ª, Á¦°ÅµÇ¾îÁú¼ö ÀÖ´Ù.
(À̰ÍÀº ½Ä°¢°øÂ¡ ȤÀº CMP°øÁ¤¿¡¼ ´õ ¸¹Àº ½Ã°£À» ¿ä±¸ÇϰԵǴ ½É°¢ÇÔÀÌ ¹ß»ýÇÑ´Ù.)
CVD¿¡ ÀÇÇØ ÁõÂøµÇ´Â °æ¿ì¿¡´Â ÀÌ·¯ÇÑ ¹®Á¦Á¡µéÀ» ¹æÁöÇÒ¼ö ÀÖ´Ù.
¿Ö³ÄÇϸé CVD´Â ¹ÝÀÀ ¼Óµµ°¡ Á¦¾î µÉ¼ö ÀÖÀ¸¹Ç·Î °ÅÀÇ 100%ÀÇ ³ôÀº aspect ratio¸¦ °¡Áö°í ÁõÂøÀÌ µÈ´Ù.(Vol. 6ÀåÀ» ÂüÁ¶)
±×·¡¼ ³·Àº ¹è¼±Ãþ¿¡¼ ±¸¸®¹è¼±¿¡¼ÀÇ È®»ê¹æÁö¸·À» ÁõÂøÇϱâÀ§ÇØ CVD°¡ Àû¿ëµÉ°ÍÀÌ´Ù. (°è¼ÓÀûÀ¸·Î aspect ratio°¡ Áõ°¡ÇÏ´õ¶óµµ)
¾Õ¼ ³íÀÇ¿¡¼ aspect ratio°¡ Áõ°¡ÇÔ¿¡µû¶ó PVD¿¡ ÀÇÇÑ contact hole ä¿òÀÌ ´õ¿í´õ ¾î·Á¿ö Áø´Ù.
Aspect ratio°¡ ´õ¿í´õ ³ô¾ÆÁü¿¡µû¶ó ȦÀÇ Ã¤¿ò¹®Á¦´Â ´õ¿í´õ Áõ°¡ÇϰԵȴÙ.
½ºÆÛÅ͸µµÈ ¿øÀڴ ŸÄϰú ¿þÀÌÆÛ°£ »çÀ̰ø°£ÀÇ °¡½º»óÅ¿¡¼ Ãæµ¹ÀÌ ¹ß»ýÇѴٴ°ÍÀ» ±â¾ïÇ϶ó.
°Ô´Ù°¡ ½ºÆÛÅ͸µµÈ ¿øÀڴ Ÿ°Ù Ç¥¸éÀÇ °¢ ÁöÁ¡À¸·ÎºÎÅÍ ±ÕÀÏÇÏÁö ¾ÊÀº ÄÚ»çÀÎ ºÐÆ÷¸¦ °¡Áö¸ç ½ºÆÛÅ͸µÀÌ ¹ß»ýÇÑ´Ù.
ÀÌ·¯ÇÑ µÎ°¡Áö ¸ÞÄ«´ÏÁòÀÇ °á°ú·Î, ±âÁ¸ÀÇ ½ºÆÛÅ͸µ Àåºñ¿¡¼´Â ½ºÆÛÅ͸µ µÈ ¿øÀÚµéÀÌ trench ³»ºÎ·Î µé¾î°¡±âº¸´Ù´Â
´õ Å« µµ´Þ°¢À» °¡ÁüÀ¸·Î½á trenchÀÇ »ó´ÜºÎ ¸ð¼¸® ȤÀº contact hole¿¡ µµ´ÞÇϰԵȴÙ.
±×·¡¼ trench ³»ºÎÀÇ »ó´ÜºÎ ¸ð¼¸®¿¡¼ÀÇ ¹Ú¸·ÁõÂø¼Óµµ´Â ÇϴܺΠȤÀº Ãø¸éÀÇ ÁõÂø¼Óµµº¸´Ù ´õ ³ôÀ»°ÍÀÌ´Ù.
ÀÌ·¯ÇÑ °á°ú·ÎºÎÅÍ »ó´ÜºÎÀÇ °³±¸ºÎ´Â ±×¸²16-16a¿¡¼ º¸´Â°Íó·³ close-off»óÅÂ(Áï, overhang)°¡ ½ÃÀ۵ȴÙ.
±×·¡¼ ÀÌ·¯ÇÑ °æ¿ì´Â ½Ã°£ÀÌ °æ°úÇÔ¿¡ µû¶ó ±×¸²16-16b¿¡¼ º¸´Â °Íó·³ Ãø¸é°ú ÇϴܺÎÀÇ ÁõÂø¼Óµµ´Â °è¼ÓÀûÀ¸·Î ´À·ÁÁö°Ô µÉ°ÍÀÌ´Ù.
¸¸ÀÏ ÀÌ·¯ÇÑ overhangÀÌ ÃæºÐÈ÷ µÎ²¨¿öÁö°ÔµÈ´Ù¸é, ȦÀº ¿ÏÀüÈ÷ ¸·Çô¹ö¸®°Ô µÇ°í ±â°øÀÌ Á¸ÀçÇÏ°Ô µÈ´Ù.
½ÉÁö¾î ÁõÂøÀÎ °è¼ÓÀûÀ¸·Î ÀϾÁö ¾Ê°ÔµÇ¸ç, overhangÀº ÇϴܺΠ¸ð¼¸®¿¡ shadow(±×¸²ÀÚÇö»ó)¸¦ ÀÏÀ¸Å´À¸·Î½á
µµ´Þ°¢(arrive angle)Àº ÀÌ¹Ì ÃÖ¼ÒȰ¡ ÁøÇàµÇ°Ô µÉ°ÍÀÌ´Ù.(±×¸²16-16bÂüÁ¶)
±×·¡¼, ȦÀÇ ÇϴܺΠ¸ð¼¸®¿¡¼ÀÇ ¾ãÀº ÁõÂø¸·ÀÌ ÀϾ°Ô µÉ°ÍÀÌ´Ù.
È®»ê¹æÁö¸·Àº ÇϴܺΠÀü¸é¿¡¼ ±× ¿ªÈ°À» ÃæºÐÈ÷ ¼öÇàÇÒÁ¤µµ·Î ¾ã¾Æ¾ß Çϱ⿡ ÀÌ·¯ÇÑ Äڳʺο¡¼ÀÇ ¾ãÀº ÁõÂøÀº
È¿°úÀûÀÎ È®»ê¹æÁö¸·ÀÇ ±â´ÉÀ» ÀúÇØÇÒ ¼ö ÀÖ´Ù.
ÀÌ·¯ÇÑ ÇϴܺΠ¸ð¼¸® ¿¡¼ÀÇ ¾ãÀº ÁõÂø¹®Á¦¸¦ ÇØ°áÇϱâÀ§ÇØ ´Ù¾çÇÑ ¹æ¹ý(CVD¸¦ Æ÷ÇÔÇÑ)µéÀÌ ¿¬±¸µÇ¾îÁ®¿Ô´Ù.
±×·¯³ª, °³·®ÈµÈ ½ºÆÛÅ͸µ ¹ýÀÌ ¿©ÀüÈ÷ »ç¿ëµÇ°í ÀÖ´Ù. ÀÌ·¯ÇÑ Ãʱ⠰³·®ÈµÈ 2°¡Áö ¹æ¹ýÀº
Collimate ½ºÆÛÅ͹ý(¹úÁý¸ð¾çÀÇ ºø»ì±¸Á¶¹°À̶ó°í ºÒ¸®´Â collimator¸¦ Ÿ°Ù°ú ¿þÀÌÆÛ »çÀÌ¿¡ Áý¾î³Ö¾î »ç¿ë)ÇÏ´Â ¹æ¹ý°ú
long-throw ½ºÆÛÅ͸µ(Ÿ°Ù°ú ¿þÀÌÆÛ°¡ ±âÁ¸ÀÇ ¸¶±×³×Æ®·Ð ½ºÆÛÅÍ ¼Ò½ºº¸´Ù 2¹è¿¡¼ 4¹è±îÁö °Ý¸®½Ã۰í
ÇöóÁ´Â Àú¾Ð»óÅ¿¡¼ ¹ß»ý½ÃÅ´)ÀÌ ÀÖ´Ù. ±×·¯³ª, ÀÌ·¯ÇÑ µÎ°¡Áö ¹æ¹ýÀº
deep sub micron°ú dual-damascene ¹è¼±°øÁ¤¿¡¼´Â ºÎÀûÇÕÇÏ¿´´Ù. ½ÉÁö¾î 300mm ´ë±¸°æÀÇ ¿þÀÌÆÛ¿¡µµ ÀûÇÕÇÏÁö ¾Ê¾Ò´Ù.
±×·¡¼ ´õÀÌ»ó ¿©±â¼´Â ´Ù·çÁö ¾Êµµ·Ï ÇϰڴÙ.(±×·¯³ª ´õ ÀÚ¼¼ÇÑ Á¤º¸´Â vol 1,22ÆÇ 11Àå¿¡¼ ¾òÀ»¼ö ÀÖ´Ù.)
¡¡
16.3.3 ÀÌ¿ÂÈ ¸¶±×³×Æ®·Ð ½ºÆÛÅÍ ÁõÂø
CMOS¿¡¼ 0.35¥ìm(0.25¥ìm)ÀÇ via¿Í contact hole¿¡¼ÀÇ ÀûÀýÇÑ È®»ê¹æÁö¸·À» ÁõÂøÇÏ´Â 2°¡Áö ½ºÆÛÅ͸µ ±â¼úÀ» »ìÆìº¸¾ÒÁö¸¸,
3:1ÀÌ»óÀÇ aspect-ratio¸¦°¡Áö´Â 0.25¥ìm(±×¸®°í ±× ÀÌÇÏÆ÷ÇÔ)ÀÇ via¿Í hole¿¡´ëÇØ¼´Â ºÎÁ·Çß´Ù.
±×·¡¼, collimate(ȤÀº long-throw) ½ºÆÛÅ͸µ, À̸¥¹Ù ÀÌ¿ÂÈ ¸¶±×³×Æ®·Ð ½ºÆÛÅ͸µ ȤÀº I-PVD(applied materials·ÎºÎÅÍ °³¹ßµÈÀ̿ ±Ý¼Ó ÇöóÁ(IMP))°¡
Â÷¼¼´ë ULSIÀÇ È®»ê¹æÁö¸·ÁõÂøÀ» À§ÇØ °³¹ßµÇ¾î¿Ô´Ù. ÀÌ·¯ÇÑ ¹æ¹ý¿¡¼, neutral-±Ý¼Ó¿øÀÚµéÀº Ÿ°Ù°ú ¿þÀÌÆÛ»çÀÌ¿¡¼ ÀÌ¿ÂȰ¡ µÈ´Ù.
¿þÀÌÆÛ¿¡¼ÀÇ ¹ÙÀ̾´Â Àü±âÀûÀÎ °¡¼ÓÈ¿¡ ÀÇÇØ À̿µéÀÌ ¿¡³ÊÁö¿Í ¹æÇâÀÌ Á¶ÀýµÇ¾î(À§¿¡ÆÛ¿¡ ´ëÇØ ¼öÁ÷ÀûÀ¸·Î) ÁõÂøÇÑ´Ù.
À̰ÍÀ» ¼öÇàÇϱâÀ§ÇØ ¸î°³ÀÇ ½ºÆÛÅ͸µ-¼Ò½ºÀÇ ÇüŰ¡ °³¹ßµÇ¾î ¿Ô´Ù.
±×¸²16-17a´Â »ó¿ëÈµÈ I-PVDÀåºñÀÎ ÀÌ¿ÂÈ ¸¶±×³×Æ®·Ð ½ºÆÛÅÍÀÇ Ã¨¹ö¸¦ µµ½ÄÈÇѰÍÀÌ´Ù.
±âÁ¸ ¸¶±×³×Æ®·Ð ¼Ò½º(DC Àü¿ø°ø±Þ)´Â Ÿ°ÙÀ¸·ÎºÎÅÍ neutral ±Ý¼Ó¿øÀÚ°¡ ¹ß»ýµÈ´Ù.(¸¶±×³×Æ®·ÐÀº Ÿ°ÙÁÖÀ§¿¡ ÇöóÁ¿Í dark space¸¦ ¹ß»ý½ÃŲ´Ù.)
±×·¯³ª, rfÀü¿ø(¼ö³Ã°¢¹æ½Ä)Àº ±×¸² 16-17bó·³ è¹ö³»¿¡¼ À§Ä¡ÇÑ´Ù.
ÀÌ ÄÚÀÏÀº ICP ¿¡ÀÇÇØ 13.56Mhz rfÀü¿ø°ø±ÞÀ¸·ÎºÎÅÍ secondary ÇöóÁ¸¦ ¹ß»ýÇÑ´Ù.
è¹ö³»ÀÇ ¾Ð·ÂÀ» 20~40mtorr±îÁö ¿Ã¸²¿¡µû¶ó secondary ÇöóÁÀÇ ±íÀÌÁ¤µµ´Â (À½±Ø°ú wafer chuck°£ÀÇ °Å¸®°¡ Áõ°¡ÇÔ¿¡µû¶ó) 8~10cm±îÁö Áõ°¡ÇÑ´Ù.
¿þÀÌÆÛ¿¡ µµ´ÞÇÑ ½ºÆÛÅÍµÈ ¿øÀÚ¿¡ ÀÇÇÑ Ãæµ¹ÀÇ È½¼ö°¡ (°¡½º»óŸ¦ ÅëÇÑ À̵¿½Ã°£ÀÌ Áõ°¡ÇÔ°ú °°ÀÌ) Áõ°¡µÈ´Ù.
ÀÌ·¯ÇÑ ±ä À̵¿½Ã°£°ú ÀÌ¿ÂÈµÈ ±Ý¼Ó¿øÀÚµéÀÇ Æ÷ÅÙ¼ÈÀº ¾Æ¸£°ï ¿øÀÚº¸´Ù ÈξÀ³·À½À¸·Î½á secondary ÇöóÁ¿¡ ÀÇÇÑ
±Ý¼Ó¿øÀÚÀÇ ÀÌ¿ÂȰ¡ ´õ¿í °¡¼ÓÈ µÈ´Ù.(¿¹: Ti ½ºÆÛÅ͸µ °øÁ¤ÀÇ °æ¿ì, ÀϹÝÀûÀ¸·Î 50~70% Ti¿øÀÚ°¡ ÀÌ¿ÂÈ µÈ´Ù.)
±×·¡¼ Áß°£Á¤µµÀÇ ¹Ðµµ¸¦ °¡Áø secondaryÇöóÁ´Â ¿þÀÌÆÛ¿Í À½±Ø»çÀÌÁö¿ª¿¡¼ ¹ß»ýÇÏ°Ô µÈ´Ù.(5x1011~1012 ions/cm©ø)
ÀÌÁ¦ I-PVDÀÇ ÁÖ¿äÀåÁ¡µéÀ» »ìÆìº¸ÀÚ. ¿þÀÌÆÛÀÇ ³×°ÅƼºê-¹ÙÀ̾¸¦ Àΰ¡ÇÔÀ¸·Î½á,
ÀÌ¿ÂÈµÈ ¸ÞÅ»¿øÀÚµéÀº ¿þÀÌÆÛ¸¦ ÇâÇØ °¡¼ÓÈ ÇÒ ¼ö ÀÖÀ»°ÍÀÌ´Ù.
±×·¡¼ ±Ý¼ÓÀ̿µéÀº ¿þÀÌÆÛ Ç¥¸é¿¡ Á¤È®ÇÏ°Ô µµ´ÞÇÑ´Ù. °Ô´Ù°¡ ¿þÀÌÆÛ-¹ÙÀ̾ Àü¿ø°ø±ÞÀº ±Ý¼ÓÀ̿µ鿡°Ô ¿îµ¿¿¡³ÊÁö¸¦ ÁְԵǾî
¿þÀÌÆÛ¿¡ ÀÌ·¯ÇÑ ±Ý¼ÓÀ̿µéÀÌ µµ´ÞÇÏ°Ô Á¦¾îÇÑ´Ù.
¿þÀÌÆÛÀÇ Àý¿¬¸é(ȤÀº ¿þÀÌÆÛ Èĸé)ÀÇ ¹ÙÀ̾ÀÇ ¹®Á¦¸¦ ±Øº¹Çϱâ À§ÇØ rf-Àü¿ø°ø±ÞÀ» »ç¿ëÇÏ¿© ÀÌ·¯ÇÑ ¹®Á¦¸¦ ÇØ°áÇÏ¿´´Ù.
¿þÀÌÆÛÀÇ ÀÌ¿Â-Ç÷°½º´Â ¼ö³ÃÁ¤µµ¿¡ µû¶ó ¾à 25¿ÍÆ®~¼ö¹é ¿ÍÆ®ÀÇ Àü¿ø°¨¼ÒÀÇ °á°ú¸¦ °¡Á®¿Ô´Ù.
I-PVD¸¦ »ç¿ëÇÑ ³ôÀº aspect-ratioÀÇ ÇϴܺΠÁõÂøÀº collimator¸¦ ÀÌ¿ëÇÑ °æ¿ìº¸´Ù ´õ¿í ÁÁÀº°ÍÀ» º¼¼ö ÀÖ¾ú´Ù.
À̰ÍÀº 8:1ÀÇ aspect ratio¿Í 0.18¥ìmÀÇ È¦¿¡¼ 40~80% ÇϴܺΠÁõÂø¿¡ µµ´ÞÇß´Ù.
ÇϴܺΠÁõÂøÀ²Àº ³ôÀº¹Ý¸é, (±×¸² 16-18ÂüÁ¶; ºñ·Ï Ãø¸éºÎÀÇ ÁõÂøÀÌ °è¼Ó µÇÁö¸¸) Ãø¸é ÁõÂøÀº ´õ¿í ¾ã´Ù´Â°ÍÀ» ÀÎÁöÇ϶ó.
I-PVD°øÁ¤ÀÇ ¸î°¡Áö ´Ù¸¥ ÀåÁ¡À» »ìÆìº¸°Ú´Ù.
ù°, collimate ½ºÆÛÅ͸µº¸´Ù ÈξÀ ¿ì¼öÇÑ Å¸ÄÏ-½Ã½ºÅÛ(colimate¿¡ ÀÇÇÑ °£¼·´ë½Å, ¿þÀÌÆÛ Ç¥¸é¿¡ µµ´ÞÇÏ´Â ´ëºÎºÐÀÇ ½ºÆÛÅÍµÈ ¿øÀÚ)À» ÇÒ¼ö ÀÖ¾ú´Ù.
±×·¡¼ ½ºÆÛÅ͸µ ¼öÀ²À» ³ôÈú¼ö ÀÖ¾ú´Ù.
µÑ°, ³ôÀº fulx¸¦ °¡Áö´Â ±Ý¼Ó ÀÌ¿ÂÀº ¿þÀÌÆÛ¿¡ ´ëÇØ ¼öÁ÷ÀûÀ¸·Î ¹èÇâµÇ¾î ȦÀÇ »ó´ÜºÎ ¸ð¼¸®¿¡¼
overhangÀ» Àç ½ºÆÛÅ͸µÇÑ´Ù. ÀÌ·¯ÇÑ °ÍÀº ȦÀÇ »ó´ÜºÎ¿¡¼ closing-upÀ» À¯Áö½ÃÄÑÁÙ¼ö ÀÖ´Ù.
±×¸² 16-18Àº I-PVD¿¡ ÀÇÇÑ ³ôÀº aspect-ratioÀÇ ÇÏ´ÜºÎ¿Í Ãøº®¸éÀÇ ÁõÂøÀ» º¸¿©ÁØ´Ù.
¼Â°, ¿þÀÌÆÛ¿¡ Àΰ¡µÈ ³×°ÅƼºê ¹ÙÀ̾´Â ÀÌ¿ÂÈµÈ ±Ý¼Ó¿øÀÚ¸¦ viaÀÇ ÇϴܺαîÁö Ãæµ¹ÇÏ°Ô ÇÒ»Ó¸¸¾Æ´Ï¶ó
±Ý¼ÓÀÌ¿Â(ȤÀº ¾Æ¸£°ïÀÌ¿Â)µéÀÌ ¿îµ¿¿¡³ÊÁö¸¦ °¡Áö°í ¿þÀÌÆÛ¿¡ bombard(Ãæµ¹)À» ÀÏÀ¸Å²´Ù.
ÀûÀýÇÑ ¹ÙÀ̾ÀÇ ¼öÁØ¿¡¼´Â ¹è¼±±¸Á¶ÀÇ Çϴܺο¡ Àç ½ºÆÛÅ͸µÀ» ÀÏÀ¸ÄѼ ÀûÀº Ãø¸éºÎÀÇ ÁõÂø¿¡´ëÇØ ÀçºÐ¹èµµ ÇÒ¼ö ÀÖ´Ù.(±×¸²16-19ÂüÁ¶)
Á¤È®È÷ collimate¿Í long-throw PVD¿¡¼ °¡Àå ÀûÀº ÁõÂøÀÌ ÀϾÙ.
ºÎºÐÀûÀÎ Àç ½ºÆÛÅ͸µÀº ÁõÂøµÈ°ÍÀ» Á¤µµ¿¡µû¶ó ÀÏÁ¤ÇÏ°Ô Àç´ÜÇϴµ¥ ÀÌ¿ëµÈ´Ù.
±×¸®°í ÀÌ·¯ÇÑ ½ºÆÛÅ͸µÀº È®»ê¹æÁö¸· ÁõÂø»Ó¸¸¾Æ´Ï¶ó seedÃþÀÇ ÁõÂø¿¡ ³Î¸® ÀÌ¿ëµÈ´Ù.
I-PVDÀÇ °³³äÀÌ ¾Õ¼ ±â¼úÇѰÍó·³ ¸¹Àº ÀåÁ¡À» °¡Áö°í ÀÖ´Â ¹Ý¸é, ³»ºÎ ÄÚÀÏ-Çü»óÀº ½ÇÁ¦ÀûÀ¸·Î »ó´çÈ÷ º¹ÀâÇÏ´Ù.
ù°, ÄÚÀÏÀº ½ºÆÛÅ͸µ Ÿ°ÙÀÇ ¹°Áú·Î ÄÚµùµÇ¾îÁú¼ö ÀÖ´Ù. ¸¸ÀÏ ³Ê¹« µÎ²®´Ù¸é flakeÇüÅ·Π¶³¾îÁ®¼ ÆÄƼŬÀ» ¹ß»ý½ÃŲ´Ù.
µÑ°, ÄÚÀÏ ÀÚü·ÎºÎÅÍ ³ª¿Â ¹°Áúµµ ½ºÆÛÅ͵ɼö ÀÖ´Ù.ÀÌ·±¹°ÁúÀº ¿þÀÌÆÛ¿¡ ¸¶Áö¸·¿¡ ÀçÁõÂø µÉ¼ö ÀÖ´Ù.
±¸¸®ÄÚÀÏÀº ±¸¸®-seed ÁõÂø°øÁ¤½Ã ÀÌ·¯ÇÑ ¹®Á¦¸¦ ÀÏÀ¸Å³¼ö ÀÖ´Ù.
Ta ȤÀº TiÀÇ ÁõÂø°úÁ¤½Ã À̰ÍÀº µ¹ÀÌų¼ö ¾ø´Ù. ´ë½Å¿¡ ÄÚÀÏÀ» Ta ȤÀº Ti·Î ¸¸µå´Â°ÍÀÌ ÇÊ¿äÇÏ´Ù.
±×·¯³ª, ÀÌ·¯ÇÑ ÄÚÀÏ(³Ã°¢¼öÀÇ À¯·®¿¡´ëÇØ¼µµ ¿ª½Ã °í·ÁÇÊ¿ä)Àº °íÁ¤µÈ°ÍÀº ¾Æ´Ï´Ù.2°¡Áö ´Ù¸¥ I-PVD¼Ò½ºÀÇ Çü»óÀº ÃÖ±Ù »ó¿ëȵǾî Ãâ½ÃµÇ¾ú´Ù.
¡¡
16.3.4 Hollow -À½±Ø ¸¶±×³×Æ®·Ð ½ºÆÛÅ͸µ ¼Ò½º
Hollow -À½±Ø ¸¶±×³×Æ®·Ð ½ºÆÛÅ͸µ(HCM)Àº Novellus INOVA ½ºÆÛÅ͸µ ½Ã½ºÅÛ¿¡¼ ¸¸µé¾îÁ³´Ù (±×¸² 16-20ÂüÁ¶).
±×¸²À» º¸¸é ¿þÀÌÆÛ¿¡ µµ´ÞÇÏ´Â ÀÌ¿ÂÈ ¸¶±×³×Æ®·Ð ½ºÆÛÅ͸µ ½Ã½ºÅÛ°ú ºñ½ÁÇÑ ÀåÄ¡ÀÌ´Ù.
ÀÏÁ¤ÇÑ ÇöóÁ¸¦ ¹ß»ýÇÏ´Â ÄŸð¾çÀÇ Hollow -À½±Ø ¸¶±×³×Æ®·Ð ½ºÆÛÅ͸µ ŸÄÏÀº Ÿ°Ù Ç¥¸éÀÇ Å« ºÐÀ²·Î ½ºÆÛÅ͸µÀ» °¡´ÉÇÏ°Ô ÇÑ´Ù.
ÀÌ·¯ÇÑ ÄŸð¾çÀÇ Å¸°Ù Çü»ó¿¡ ÀÇÇØ è¹ö º®¸é¿¡ ÁõÂøµÇ´Â°Í ´ë½Å¿¡ neutralÀÇ »ó´çÇÑ ºÐÀ²ÀÌ Å¸°ÙÇ¥¸é¿¡¼ Àç ÁõÂøµÈ´Ù.
À̰ÍÀº ³ôÀº Ÿ°ÙÀÇ È°¿ëÀÇ ÀÕÁ¡À» Á¦°øÇÑ´Ù. °Ô´Ù°¡ °í¹ÐµµÀÇ ÇöóÁ¸¦ ¹ß»ý½Ãų ³»ºÎÀÇ rf-ÄÚÀÏÀÌ ÇÊ¿äÇÏÁö ¾Ê´Ù.
´ë½Å¿¡ ¿µ±¸ÀÚ¼®ÀÇ ¹èÇâÀÌ Å¸°Ù¿¡ ÀÇÇØ ½ºÆÛÅÍµÈ ´ºÆ®¶öÀÇ ÀÌ¿ÂÈ(90%ÀÌ»óÀÇ ÀÌ¿ÂÈ)¸¦ ÇÔÀ¸·Î½á ÀüÀÚµéÀ» ¹æÃâÇÏ°Ô Çß´Ù.
¿þÀÌÆÛ Ã´¿¡¼ÀÇ ¹ÙÀ̾´Â ¿þÀÌÆÛ·ÎºÎÅÍÀÇ ÀÌ¿ÂÈµÈ ½ºÆÛÅÍ ¿øÀÚµéÀ» ¼öÁ÷¹æÇâÀ¸·Î °¡¼ÓÈÇÏ¿´´Ù.
À̰ÍÀº ³ôÀº aspect-ratioÀÇ È¦À» °¡´ÉÇÏ°Ô Çß´Ù. HCMÀº Ta, TaN,TiN,CuÀÇ ½ºÆÛÅ͸µ ÁõÂø¿¡ »ç¿ëµÉ¼ö ÀÖ´Ù.
¡¡
16.3.5 self-ÀÌ¿ÂÈ ÇöóÁ ½ºÆÛÅ͸µ ¼Ò½º
I-PVD±â¼úÀ» ´ëüÇÒ ¶Ç´Ù¸¥ »õ·Î¿î ½ºÆÛÅ͸µ Àåºñ´Â ÃÖ±Ù ¾îÇöóÀÌµå ¸ÓÆ¼¸®¾ó»ç¿¡ ÀÇÇØ °³¹ßµÇ¾ú´Ù.
À̸§ÇÏ¿© SIP(self-ÀÌ¿ÂÈ ÇöóÁ ½ºÆÛÅ͸µ)ÀÌ´Ù. ±×¸®°í À̰ÍÀº IMP¿¡¼ ¸ÞÅ»¿øÀÚÀÇ ÀÌ¿ÂÈ¿¡ ÇÊ¿äÇÏ¿´´ø rf-ÄÚÀÏÀÇ »ç¿ëÀÌ ÇÊ¿äÄ¡ ¾Ê¾Ò´Ù.
ÀÌ·¯ÇÑ ¼Ò½º¿¡°üÇØ ¸¹ÀÌ Á¦½ÃµÇÁö ¾Ê¾ÒÁö¸¸, ¸î¸î¿¡ °üÇØ ¼³¸íµÇ¾ú´Ù.
ÀÌ ¼Ò½º´Â »ó´ëÀûÀ¸·Î ³·Àº ¾Ð·Â(2mTorrÀÌÇÏ)¿¡¼ Ÿ°Ù°ú ¿þÀÌÆÛ°£ÀÇ °Å¸®°¡ ±âÁ¸ ¸¶±×³×Æ®·Ð ½ºÆÛÅÍ ¼Ò½º¿¡ ºñÇØ ´õ ±æ¾îÁ® ¿î¿ëµÈ´Ù.
À̰ÍÀº ±Ý¼ÓÀÌ¿ÂÀÇ mean free path (Æò±ÕÀÚÀ¯Çà·Î)¸¦ Áõ°¡½Ã۰í, ±Ý¼ÓÀÌ¿ÂÀÇ self-collimationÀ» Á¦°øÇÑ´Ù.
self-ÀÌ¿ÂÈ ÇöóÁ´Â ¼Ò½º¿¡ ÀÇÇØ ½ºÆÛÅÍµÈ ±Ý¼Ó¿øÀÚµéÀÌ ÀÌ¿ÂÈ µÊÀ» ½Ã»çÇϰí,
´Ù¸¥ ±Ý¼Ó¿øÀÚ¿¡ ÃæºÐÇÑ ¿¡³ÊÁö¸¦ °¡Áö°í Ÿ°ÙÀ¸·Î µÇµ¹¾Æ °£´Ù.±×¸®°í ¶ÇÇÑ Ãß°¡ÀûÀÎ ÀüÀÚ¸¦ ¹ß»ýÇÑ´Ù.
ÀÌ·¯ÇÑ Ãß°¡ÀûÀÎ ÀüÀÚÀÇ ½ºÆÛÅÍµÈ ±Ý¼Ó¿øÀÚÀÇ ÀÌ¿Âȸ¦ ¹ß»ýÇϰí, self-ÀÌ¿ÂÈ ÇöóÁ¸¦ À¯ÁöÇÏ¸é¼ º¸´Ù ´õ ¸¹Àº ±Ý¼ÓÀÌ¿Âȸ¦ À¯µµÇÑ´Ù.
ÀÌ·¯ÇÑ Çö»óÀº ¸í¹éÇÏ°Ô ±¸¸®¿Í °°Àº ÀÌ¿ÂÈ ¿¡³ÊÁö°¡ ÀÛÀº ±Ý¼Ó¿øÀÚ¸¦ È¿°úÀûÀ¸·Î ÀÌ¿ÂȽÃŲ´Ù.
±×·¯³ª Ta°ú °°Àº ³ôÀº ÀÌ¿ÂÈ ¾î³×Áö¸¦ °¡Áö´Â ±Ý¼Ó¿øÀÚ¿¡´ëÇØ¼µµ Àû¿ëµÇ µÉÁö´Â Àǹ®½Ã µÇ°í ÀÖ´Ù.
16.3.6 TaÀÇ ¹°¼º°ú ¹ÝµµÃ¼ Àû¿ëÀ» À§ÇÑ Á¤Á¦µÈ Ta
Ta(ȤÀº Ta¿¡ ±âÃÊÇÑ TaN, TaSiN)Àº Cu-damascene°øÁ¤¿¡¼ È®»ê¹æÁö¸·À¸·Î ³Î¸® »ç¿ëµÇ¾î¿À°í ÀÖ´Ù. ÀÌ·¯ÇÑ ÀÌÀ¯·Î ÀÌ·¯ÇÑ ¿ø¼Ò¿¡ ´ëÇÑ »ç¿ë¹è°æÀ» »ìÆìº¸ÀÚ.
16.3.6.1 TaÀÇ ¹°¼º
TaÀº ¿øÀÚ¹øÈ£ 73ÀÇ À籸¼ºµÈ ±Ý¼Ó¿ø¼ÒÀÌ´Ù.¿øÀÚÁú·®Àº ¾à 181À̸ç, BCC(ü½ÉÀÔ¹æ)±¸Á¶¸¦ °¡Áö°í ÀÖ´Ù.
±×¸®°í ȸ»öÀÇ »ö±òÀ» ¶ç°íÀÖ´Ù. À̰ÍÀº ³ôÀº À¶Á¡(2996¢ªC)À» °¡ÁüÀ¸·Î½á CuÀÇ È®»ê¹æÁö¸·À¸·Î ³Î¸® »ç¿ëµÇ¸ç, À̰ÍÀº ±¸¸®¿Í È¥ÇÕÇÏÁö ¾Ê±â¿¡ »ç¿ë°¡´ÉÇÏ´Ù.
¶ÇÇÑ ±Ý¼Ó-»ê¼Ò°£ °áÇÕ°ú ¸Å¿ì ³ôÀº ±Ý¼Ó°£º»µùÀÌ °ÇÏ°Ô Çü¼ºµÈ´Ù. ±×·¡¼ À̰ÍÀº ³·Àº Á¢ÃËÀúÇ×°ú ±¸¸®¿¡´ëÇØ ÁÁÀº Á¢Âø·ÂÀ» °¡ÁöÀÖ´Ù.
¾ÆÁ̷ֹ®ÀÇ Áú¼Ò¸¦ ÀÌ¿ëÇÑ TaÀÇ µµÇÎÀº È®»êÇà·Î¸¦ ¸·À» ¼ö ÀÖ´Ù. TaN(Áú¼ÒºÐÀ§±â¿¡¼ ½ºÆÛÅÍÇÑ °æ¿ì ¹ÝÀÀÇÑ)µµ
¿ª½Ã È®»ê¹æÁö¸·À¸·Î¼ »ç¿ëµÈ´Ù.TaNÀº ´ÙÀ½¿¡ ³íÀÇ µÉ °ÍÀÌ´Ù.
¡¡
16.3.6.2 ½ºÆÛÅ͸µ Ÿ°Ù TaÀÇ Á¦Á¶¿Í Á¤Á¦
ÀÚ¿¬»óÅ¿¡¼´Â Ta2O5·Î Á¸ÀçÇÑ´Ù. TaÀÇ Ãµ¿¬±¤¹°Àº tantalite(Fe,Mn)Ta2O5ÀÌ´Ù.
¿À½ºÆ®¸®¾Æ ¼ºÎ´Â °í¼øµµÀÇ TaÀÇ ÃÖ´ë Á¦Á¶¾÷üÀ̸ç, ÀÌ·¯ÇÑ ¼øµµÀÇ ±¤¹°Àº TaÁ¦Á¶¾÷ü·Î Á¤Á¦µÇ±â À§ÇØ ¼ö¼ÛµÈ´Ù.
Á¤Á¦µÈ TaÀÇ ÁÖ¿ä ½ÃÀåÀº capacitorµî±Þ ºÐ¸»(50%), Ta¼±°ú ºÐ¼âÁ¦Ç° (16%), ÈÇÐÀû º¹ÇÕ¹°(źŻ·ý Ä«¹ÙÀ̵å)°¡ 14%,
±Ý¼ÓÇձݹ° ÷°¡Á¦(6%)·Î ÀÌ·ç¾îÁ®ÀÖ´Ù. ½ºÆÛÅ͸µ Ÿ°Ù°ú °°Àº °í¼º´ÉÀÇ TaÁ¦Ç°Àº Ta ¿ÍÀ̾î¿Í ¹Ð¸µ Á¦Ç°ÀÇ 10%¸¦ Â÷ÁöÇϰí ÀÖ´Ù.
Tatalite ±¤¼®¸¸ÀÌ TaÀÇ Àç·á°¡ ¾Æ´Ï´Ù. °ÅÀÇ TaÀÇ ÃÑ»ç¿ë·®ÀÇ 25%°¡ ÀçȰ¿ëµÇ°í ÀÖ´Ù.
»ç½Ç»ó °í¼øµµÀÇ ½ºÆÛÅ͸µ Ÿ°ÙÀ» À§ÇÑ ½ÃÀåÀº Á¡Â÷ Áõ°¡ Çϰí ÀÖ´Ù.
¾ÕÀ¸·Î´Â ¹ÝµµÃ¼ °øÁ¤¿¡¼ÀÇ TaŸ°ÙÀÌ ÇʼöÀûÀÌ¸ç ¸¹Àº ºÎ¹® Á¡À¯ÇÒ°ÍÀÌ´Ù.
TaÀÇ Á¤Á¦°øÁ¤°ú ÃßÃâÀº ºÐ¸»»óÅ¿¡¼ Ta¸¦ ÈÇÐÀû ħ° ½ÃÄÑ ¾ò´Â´Ù.
ÀçȰ¿ëµÈ TaÀÇ °í¹Ðµµ, °í¼øµµ ºÐ¸»Àº Áø°ø¿ëÇØ·Î¼ ¾ò´Â´Ù.(Ta´Â »ê¼Ò,Áú¼Ò¿Í ź¼Ò¿¡ ¹ÝÀÀÀ» Çϸç, ¿Ã³¸®´Â Áø°ø ȤÀº ºÒȰ¼º°¡½º¿¡¼ ÀÌ·ç¾îÁ®¾ß±â ¶§¹®¿¡)
½ºÆÛÅÍ¿Í °°Àº ÁõÂø¿¡¼ ¿ä±¸µÇ´Â ÀÀ¿ëÀ» À§ÇØ Á¤Á¦µÈ Ta°¡ ÇÊ¿äÇϰí, À̰ÍÀº Áø°ø¿ëÇØ°øÁ¤¿¡¼ TaºÐ¸»¿¡ ÀÇÇØ ¾ò¾îÁú¼ö ÀÖ´Ù.
ÀϹÝÀûÀ¸·Î, Ta À×°÷Æ®(À×°÷Æ®¶õ: ¿ø·á·Î ±¸¼ºµÈ ¸·´ëºÀÀ» ¶æÇÔ)´Â ºÒ¼ø¹°ÀÇ Á¤Á¦¸¦ À§ÇØ ¿©·¯Â÷·Ê ³ìÀÌ°Ô µÈ´Ù.
ÀÌ·¯ÇÑ ÀÌÀ¯´Â TaÀÇ ³ì´ÂÁ¡ÀÌ ´ëºÎºÐ ´Ù¸¥±Ý¼Óµéº¸´Ù ³ô±â¶§¹®ÀÌ´Ù.
±×¸®°í, ħÀÔÇü °¡½º(»ê¼Ò, Áú¼Ò, ź¼Ò)¿¡¼ ¸¹Àº ºÒ¼ø¹°ÀÌ ¹ß»ýÇÑ´Ù.
±×·¯³ª, ´Ù¸¥¿ø¼Ò¿ÍÀÇ Àç°áÇÕ(Áï, ´Ï¿Àºç, ¸ô¸®ºêµ§, ÅÖ½ºÅÙ°ú °°Àº)¿¡ ÀÇÇØ Áø°ø¿ëÇØµ¿¾ÈÀº À̵éÀÌ Èñ¹ßµÇÁö ¾Ê´Â´Ù.
ÇÏÁö¸¸ À̵éÀº ³ìÀ»¼ö ÀÖ´Â ºÒ¼ø¹°·Î½á Ta³»¿¡ Á¸ÀçÇϰԵȴÙ.
ÇÏÁö¸¸ ÀÌµé ±Ý¼Ó¿À¿°ÀûÀÎ Àç°áÇÕ¹°Àº Ư¼ºÈµÈ front-end ÈÇÐÃßÃâ°øÁ¤¿¡ ÀÇÇØ ÁÙ¿©Áú¼ö ÀÖÀ¸¸ç,
ÃÖÁ¾ÀûÀ¸·Î ÃÖÁ¾ÀûÀ¸·Î ¼ø¼öÇÑ TaÀÇ À×°÷Æ®¸¦ ¾òÀ»¼ö ÀÖ´Ù.
¿¹¸¦µé¸é Cabot ¹°¼º¿¡ °üÇÑ ÇÑ ºÎ¼´Â 99.999%ÀÇ ¼øµµÀÇ Ta À×°÷Æ®¸¦ ¿ä±¸ÇÑ´Ù.
ÀÌ·¯ÇÑ ¼ø¼öÇÑ À×°÷Æ®´Â ÀÛÀº Å©±âÀÇ °áÁ¤¸³À» °¡Áø ´Ù°áÁ¤ Ta·Î ±¸¼ºµÇ¾î ÀÖ´Ù.
ÀÌ·¯ÇÑ À×°÷Æ®´Â ÃÖÁ¾ ¾î´Ò¸µ °øÁ¤¿¡¼ °áÁ¤¸³ ±¸Á¶¸¦ Àç°áÁ¤È ÇϱâÀ§ÇØ Àý´ë¿Âµµ¿¡¼ ³Ã°¢ °øÁ¤Ã³¸®°¡ µÈ´Ù.
Ta ½ºÆÛÅ͸µ Ÿ°ÙÀ» À§ÇÑ ¹Ì¼¼Á¶Á÷±¸Á¶´Â ÀÛÀº°ÍÀ» ¿ä±¸Çϸç, ±ÕÀÏÇÑ ´Ù°áÁ¤ ±¸Á¶¸¦ ¿øÇÑ´Ù.
Ta °áÁ¤ grainÀº (111) ȤÀº (001)À¸·Î ±¸Á¶¸¦ °¡Áø´Ù. TaÀÇ À×°÷Æ®´Â (111)¹æÇâÀ¸·Î ÁÖ·Î ¹è¿µÇ±â ¼±È£ÇÑ´Ù.
ÀÌ·¯ÇÑ ÀÌÀ¯´Â (001)Ŭ·¯½ºÅ͸¦ °¡Áö´Â Ta½ºÆÛÅÍ Å¸°Ù¿¡¼´Â ½ºÆÛÅ͵Ǵ ¼öÀ²ÀÌ ³·±â¶§¹®À̰í,
Ta´Â BCC(ü½ÉÀÔ¹æÁ¤±¸Á¶)À̸ç, À̰ÍÀº ºÎ½ÄÀ²ÀÌ (111)¿¡°üÇØ ÀϾ´Â°ÍÀÌ (001)À¸·Î ÀϾ´Â °Íº¸´Ù ´õ¿í Áõ°¡µÇ±â ¶§¹®ÀÌ´Ù.
(111):(001)ÀÇ grain ºñÀ²Àº º¯Çü»ç¿¡ ÀÇÇØ ´Ù·ç¾îÁø´Ù.
¿ä¾àÇÏÀÚ¸é, ¿ÈÇÐÀû °øÁ¤À» ÅëÇØ ¾òÀº Ta ½ºÆÛÅ͸µ Ÿ°Ù¿¡¼ÀÇ ±ÕÀÏÇÑ Á¶Á÷Àº Ÿ°ÙÀÇ Æ¯¼º¿¡¼ ¸Å¿ì Áß¿äÇÏ´Ù.
¿ÈÇÐÀû °øÁ¤°ú Á¤Á¦°øÁ¤Àº ¸Å¿ì ºñ½Ñ °øÁ¤ÀÓÀ» ±â¾ïÇ϶ó ±× °á°ú ¶ÇÇÑ Ta ½ºÆÛÅ͸µ Ÿ°ÙÀº ¸Å¿ì ºñ½Î´Ù. (4¸¸´Þ·¯ ȤÀº ±×ÀÌ»ó)
¡¡
16.3.6.3 CuÈ®»ê¹æÁö¸·À¸·Î½á Ta, TaN¿Í TaSiNÀÇ ¹°¼º
Cu ¿øÀÚÀÇ È®»ê À̵¿À» ¸·±âÀ§ÇØ È®»ê¹æÁö¸·Àº Cu¿Í ¹ÝÀÀÇÏÁö ¾Ê¾Æ¾ß ÇÑ´Ù.
ÀÏ´Ü Cu°¡ ÁõÂøµÈ ¿þÀÌÆÛ¿¡¼ÀÇ È®»ê¹æÁö¸·Àº ÃÖ´ë¿Âµµ±îÁö ¿Àû ¾ÈÁ¤È »óÅ·ΠÀ¯ÁöÇØ¾ßÇÑ´Ù.
¿Âµµ´Â 500¢ªC¸¦ ÃʰúÇÏÁö ¾ÊÀ¸¸ç, È®»ê¹æÁö¸·Àº ÀÌ ¿Âµµ¿¡¼ ¾ÈÁ¤È µÉ°ÍÀÌ´Ù.
Ta¿Í TaN¹Ú¸·Àº 550¢ªC±îÁö¿¡¼µµ ¿ÀûÀ¸·Î ¾ÈÁ¤ÇÔÀÌ °üÂûµÇ¾ú´Ù. ±×¸®°í À̵éÀº back-end°øÁ¤¿¡¼µµ ÀûÇÕÇÏ¿´´Ù.
±×·¯³ª, 16.1Àý¿¡¼ º» °Íó·³ È®»ê¹æÁö¸·Àº CuÀÇ Á¢Âø¸·À¸·Î ÀÛ¿ëÇØ¾ßÇϱ⿡ À̵é È®»ê¹æÁö¸·Àº È®»ê¹æÁö¿Í Cu¿Í Á¢Âø´É·ÂÀ» °¡Á®¾ßÇÑ´Ù.
¸¸ÀÏ È®»ê¹æÁö¸· ¹°ÁúÀÌ Cu¿Í ÀüÇô ¹ÝÀÀÀÌ ¾ø´Ù¸é, Á¢Âø·ÂÀÌ ¾øÀ»°ÍÀÌ´Ù.
¸¸¾à, ÀÌµé ¹°ÁúÀÌ ³Ê¹« ½±°Ô ¹ÝÀÀÇÑ´Ù¸é, À̰ÍÀº È®»ê¹æÁö¸·À¸·Î Á¦ ±â´ÉÀ» ´ÙÇÏÁö ¸øÇÒ°ÍÀÌ´Ù.
ÁÁÀº È®»ê¹æÁö¸· Ư¼º°ú ±¸¸®¿Í ÁÁÀº Á¢Âø·ÂÀ» À§Çؼ´Â ÀÌ»óÀûÀÎ È®»ê ¹æÁö¸·Àº Cu¿Í self-limitingÀûÀ¸·Î ¹ÝÀÀÇØ¾ß ÇÑ´Ù.
Ta¹Ú¸·¿¡¼, ArºÐÀ§±â¿¡¼ Ta Ÿ°ÙÀ» »ç¿ëÇÏ¿© ½ºÆÛÅÍÇÏ¿© ±¸¸®¿¡´ëÇÑ È®»ê¹æÁö¸·À» Á¶»çÇÏ¿´´Ù.
TaÀǰæ¿ì Ta ¹Ú¸·À§¿¡ ±¸¸®ÃþÀÌ ÁõÂøµÈ »óÅ·Π°è¸éÀ» º¸¿´´Ù.
±×·¯³ª, 3nmµÎ²²ÀÇ ºñÁ¤Áú ÃþÀÌ 400¢ªC ¿¡¼ 1½Ã°£µ¿¾È ¾î´Ò¸µ ÇÑ ÈÄÀÇ Ta/Cu°è¸é¿¡¼ °üÂûµÇ¾ú´Ù.
ÀÌ·¯ÇÑ ºñÁ¤Áú ÃþÀÇ ¸ÞÄ«´ÏÁòÀº Ta°¡ 400¢ªC¿¡¼ Cu¿¡ ÆòÇü¿ëÇØµµ¸¦ °¡ÁöÁö ¾Ê±â¿¡ ¸íÈ®È÷ ÀÌÇØµÇÁö ¾Ê¾Ò´Ù.
±×¸®°í, ±¸¸®¿Í º¹ÇÕ¹°À» Çü¼ºÇÏÁö ¾Ê¾Ò´Ù. ±×·³¿¡µµ ºÒ±¸Çϰí, ÀÌ ºñÁ¤Áú ¹Ú¸·Àº Ta¿Í Cu¿¡ Á¢Âø·ÂÀ» Çâ»ó ½ÃŲ´Ù°í »ý°¢µÈ´Ù.
°Ô´Ù°¡ TaÀÇ ¹Ú¸·Àº 111¹æÇâÀ¸·Î ÁõÂøµÈ CuÀÇ ÇÙ »ý¼º¸·À» »ý¼ºÇϴµ¥ ÀÕÁ¡À» °¡Áø´Ù.
±×·¯³ª, TaÀÇ È®»ê¹æÁö¸·Àº PVD¿¡ ÀÇÇØ ÁõÂøµÇ¾î ´Ù°áÁ¤ÀÇ ¹Ú¸·À» °¡Áø´Ù.
±×·¡¼ ½ÉÁö¾î 400¢ªC¿¡¼ Ta¿Í Cu»çÀÌÀÇ ¹ÝÀÀÀÌ ±Ù°Å¸®¿¡¼ ¹ß»ýÇÑ´Ù. ±¸¸®Àº źŻ·ý ¹Ú¸·ÀÇ À԰踦 µû¶ó È®»êµÇ¸ç, Àý¿¬¸·À¸·Î À̵¿Çذ£´Ù.
±×·¡¼, Ta¸¸À¸·Î´Â ÀûÀýÇÑ È®»ê¹æÁö¸·À¸·Î »ç¿ëµÉ ¼ö ¾ø´Ù.
TaNÀº Ta¿Í °ü·ÃÀÌ ÀÖ´Â ¹°ÁúÀ̸ç, À¶Á¡ÀÌ 3087¢ªCÀÇ °íÀ¶Á¡À» °¡Áö¸ç, ¹Ì¼¼Á¶Á÷±¸Á¶¿ª½Ã ´õ¿í Á¶¹ÐÇÏ´Ù.
Ta Ÿ°ÙÀ» »ç¿ëÇÏ¿© ½ºÆÛÅ͸µ °¡½º ºÐÀ§±â¿¡¼ ¾Æ¸£°ï °¡½º¿¡ Áú¼Ò¸¦ ÷°¡ÇÔÀ¸·Î½á PVD¹æ¹ýÀ¸·Î ÁõÂøÀ̵ȴÙ.
±×·¡¼ Ta´Â ¿þÀÌÆÛÀ§¿¡ ½ºÆÛÅ͵ǰԵǰí, Áú¼Ò¿Í ¹ÝÀÀÇÏ¿© TaNÀÇ ¹Ú¸·À» Çü¼ºÇÏ°Ô µÈ´Ù.
TaN¹Ú¸·Àº Taº¸´Ù ´õ¿í ¹ÝÀÀÀÇ ¹Î°¨¼ºÀÌ Àû°í ±¸¸®¿Í ¹ÝÀÀÇÏÁö ¾Ê´Â´Ù. °Ô´Ù°¡ TaNÀº Áú¼ÒÀÇ À¯·®¿¡µû¶ó ºñÁ¤ÁúÀÌ ¸¸µé¾îÁö°Å³ª,
´Ù°áÁ¤ ¹Ú¸·ÀÌ ¸¸µé¾îÁø´Ù. TaNÀº Taº¸´Ù ´õ¿í ¿ì¼öÇÑ È®»ê¹æÁö¸·À¸·Î ¾Ë·ÁÁ®¿Ô´Ù.
±×·¯³ª, TaNÀº Cu¿Í ¹ÝÀÀÇÏÁö ¾Ê¾Æ¼, À̰ÍÀº Cu¿Í Á¢Âø·Â¹®Á¦¿¡¼´Â ÁÁÁö¾Ê´Ù.
Cu-CMP°øÁ¤¿¡¼, Á¢Âø·ÂÀÇ Æ¯¼ºÀº Áß¿äÇÏ´Ù. °¢ ¹Ú¸·(Ta, TaN)ÀÇ ÀÌ·± Á¦ÇÑÁ¡À» ±Øº¹ÇϱâÀ§ÇØ
TaN/Ta, Ta/TaN/Ta¿Í °°Àº 2Ãþ,3Ãþ ¹Ú¸·À» »ç¿ëÀÌ Á¦¾ÈµÇ¾ú´Ù.
ÀÌ·¯ÇÑ ´ÙÃþ¹Ú¸·Àº Cu¹è¼±°øÁ¤¿¡ Àü¹ÝÀûÀ¸·Î ¿ä±¸µÇ¾ú´Ù. TaSiNÀº ¶Ç´Ù¸¥ ±¸¸®È®»ê¹æÁö¸· ¹°Áú·Î ´ëµÎµÇ¾ú´Ù.
À̰ÍÀº TaSi(³·Àº SiÀÇ Á¶¼º)Ÿ°ÙÀ» »ç¿ëÇÏ¿© ¾Æ¸£°ï°ú Áú¼ÒºÐÀ§±â¿¡¼ ÁõÂøµÇ¾ú´Ù.
TaSiN´Â ºñÁ¤Áú·Î Àç°áÇÕÇÏ¿´°í, ´Ù°áÁ¤ ¹Ú¸·¿¡¼ÀÇ È®»êÅë·Î·Î¼ ÀÛ¿ëÇÒ¼ö Àִ°áÁ¤À԰踦 ÀüÇô °¡ÁöÁö ¾Ê¾Ò´Ù.
À̰ÍÀº Ç϶󾾵ÀÇÇØ º¸°íµÇ¾î¿Ô´Ù.
TaSiNÀº TaN/Taº¸´Ù ´õ¿í ÁÁÀº Á¢Âø·Â°ú È®»ê¹æÁö¸·ÀÇ Æ¯¼ºÀ» º¸¿´´Ù. °Ô´Ù°¡ TaSiNÈ®»ê¹æÁö¸·À§¿¡¼ÀÇ
±¸¸®ÁõÂøÀº °°Àº (111)¹æÇâÀ¸·Î ÁõÂøµÇ¾ú´Ù.
1999-2000³â¿¡ ¹ßÇ¥µÈ 75ÆäÀÌÁö ÀÌ»óÀÇ ÀÚ·áÁ¶»ç´Â TaSiNÀÌ Ta¿Í TaNº¸´Ù ´õ¿í ³ôÀº¿Âµµ¿¡¼ È®»ê¹æÁö¸·À¸·Î ÀÛ¿ëÇÔÀ» º¸¿©ÁÖ¾ú´Ù.
±×·¯³ª, Si°¡ º¹ÇÕ¹°(TaSiN, TiSiN)·Î Á¸ÀçÇÔÀ¸·Î ÀúÇ×ÀÌ ³ô´Ù. ±×·¡¼ ¹ÝµµÃ¼Á¦Á¶¾÷ü´Â TaN ȤÀº Ta¸¦ ±¸¸®ÀÇ È®»ê¹æÁö¸·À¸·Î¼ ¼±È£ÇÑ´Ù.
¡¡
16.3.7 ´Ù¸¥ ±¸¸® È®»ê¹æÁö¸·ÀÇ ´ëµÎ
´Ù¾çÇÑ ±¸¸® È®»ê¹æÁö¸·À¸·Î¼ÀÇ ¹°ÁúµéÀÌ Á¶»çµÇ°íÀÖ°í, ´ëºÎºÐ(TiN, TiSiN, WN)µîÀÌ º»Àý¿¡¼ À̾߱âµÈ´Ù.
TiNÀº ¾Ë·ç¹Ì´½¹è¼±°øÁ¤¿¡¼ ÁÁÀº È®»ê¹æÁö¸·À¸·Î ³Î¸® »ç¿ëµÇ¾î ¿Ô´Ù.
¹Ý¸é, ±¸¸®¿¡¼ÀÇ °æ¿ì È®»ê¹æÁö¸·Àº ¿ª½Ã È®»ê¹æÁö¸·À¸·Î¼ÀÇ ¿ªÇÒÀ» ÇÏÁö¸¸,
Á¢ÂøÃþ¹Ú¸·Ãø¸éÀ¸·Î¼ Ta¸¸Å ÁÁÁö´Â ¾Ê´Ù. CVD-TiNÀº ¿©ÀüÈ÷ ±¸¸®ÀÇ È®»ê¹æÁö¸·À¸·Î °í·ÁµÇ°í ÀÖ±äÇÏÁö¸¸,
À̰͵éÀº PVD-TaN, Ta¸¸Å È¿°úÀûÀÌÁö ¾Ê´Ù. °Ô´Ù°¡ TiNÀ§¿¡¼ ÁõÂøµÈ ±¸¸®¹Ú¸·Àº TaÀ§¿¡¼ ÁõÂøµÈ ±¸¸®¹Ú¸·º¸´Ù (111)¹æÇâÀ¸·Î ¾àÇÑ ±¸Á¶¸¦ °¡Áø´Ù.
±×·¡¼, PVD ȤÀº CVD·Î ÁõÂøµÈ TiNÀº ±¸¸®¹è¼±°øÁ¤¿¡ ³Î¸® Àû¿ëµÇ°í ÀÖÁö ¾Ê´Ù.
±×·¯³ª, ALDÀÇ ÀÇÇØ ÁõÂøµÈ TiNÀº ±¸¸®¹è¼±°øÁ¤¿¡ ÀûÇÕÇÑ È®»ê¹æÁö¸·À¸·Î½á ¾ð±ÞµÇ¾î ¿Ô´Ù.
ALD¿¡ ÀÇÇÑ TiNÁõÂøÀº ÃÖ±Ù¿¡ º¸°íµÇ¾ú´Ù.
±×·¯³ª CVD¿¡ ÀÇÇØ ÁõÂøµÈ TiSiNÀº TiN¿¡ ºñÇØ »ó´çÈ÷ Çâ»óµÈ È®»ê¹æÁö¸·À¸·Î ¾Ë·ÁÁ³´Ù.
Áú¼Ò¸¦ »ç¿ëÇÏ¿© ÁõÂøµÈ TiNÀº Çâ»óµÈ È®»ê¹æÁö¸·ÀÇ ¿ªÇÒÀ» ³ªÅ¸³»¾ú´Ù.
TiSiNÀº ¿ª½Ã electromigrationƯ¼º¿¡ ÁÁÀº ±¸¸®¿¡ ´ëÇØ ÁÁÀº Á¢Âø·ÂÀ» º¸ÀδÙ.
CVD-TiSiNÀº TDMAT¿¡ÀÇÇØ ÁõÂø µÇ¾ú°í, silaneÀº ÇÁ¸®Ä¿¼·Î »ç¿ëµÇ¾ú´Ù.
(Ãß°¡ÀûÀÎ TDMAT¿¡ÀÇÇÑ CVD-TiNÀº Vol.1 6Àå 6.7.3ÀýÀ» »ìÆìº¼°Í)
CVD¿¡ ÀÇÇÑ È®»ê¹æÁö¸·ÀÇ ÁõÂøÀº 0.1¸¶ÀÌÅ©·ÎÀÌÇÏ¿¡¼ Àû¿äÀÌ °¡´ÉÇÏ´Ù.
CVD¿¡ÀÇÇØ ÁõÂøµÈ ÅÖ½ºÅÙ ³ªÀÌÆ®¶óÀÌµå ¿ª½Ã ±¸¸® È®»ê¹æÁö¸·À¸·Î °í·ÁµÇ°í ÀÖ´Â ¹°ÁúÀÌ´Ù.
Á¦ÇÑÀûÀÎ °³¹ßÀÇ CVD-WN°¡ GENUS¿¡ ÀÇÇØ 1999³â Á¦¾ÈµÇ¾ú´Ù. ±×·¯³ª, À̰ÍÀº »ó¾÷ÀûÀ¸·Î Àû¿ëÀÌ ÀûÇÕÇÏÁö ¾Ê¾Ò´Ù.
À̵éÀº ±¸¸®ÀÇ È®»ê¹æÁö¸·À¸·Î¼ PVD-Ta ȤÀº TaNº¸´Ù ´ú È¿°úÀûÀÎ ¹Ú¸·À¸·Î °áÁ¤µÇ¾îÁ³´Ù.
¡¡
*ÀÛ¼ºÀÚ : ÇѾç´ëÇб³ ±Ý¼ÓÀç·á°øÇаú ¹Ú»ç°úÁ¤ È«Àǰü
Áß°í±â°è
ÇѰø Áß°í±â°è Áß°í °øÀÛ±â°è Áß°í»ê¾÷±â°è ½Äǰ±â°è
ÇѰø±â°è
011-232-9991
ÇѰø Áß°í±â°è Áß°í °øÀÛ±â°è Áß°í»ê¾÷±â°è ½Äǰ±â°è |
|
|
|
|
|
|